引言
联轴器作为机械传动系统中的关键部件,其性能直接影响到设备的运行效率及安全性。随着工业设备向高速、重载、精密化方向发展,联轴器的检测工作显得尤为重要。本检测报告旨在通过科学的方法与先进的仪器,对联轴器的各项性能指标进行全面评估,确保其符合设计要求和实际工况需要,为设备维护和故障预防提供可靠依据。
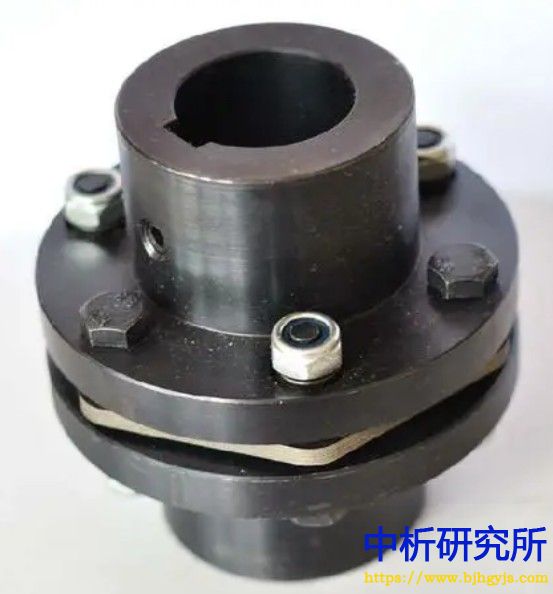
检测范围
联轴器检测适用于以下类型及场景:
- 类型覆盖:弹性联轴器、刚性联轴器、齿轮联轴器、万向联轴器等;
- 应用领域:风力发电机组、石油化工设备、船舶动力系统、轨道交通装备等;
- 检测对象:新制造联轴器的出厂检验、使用中联轴器的定期维护检测、故障后的失效分析。
检测项目
联轴器的检测需涵盖以下核心项目:
- 外观与尺寸检测:表面缺陷、几何尺寸公差、轴孔配合精度;
- 动平衡测试:高速旋转时的振动幅值与相位偏差;
- 材料性能分析:硬度、抗拉强度、耐磨性及耐腐蚀性;
- 动态特性评估:扭矩传递能力、扭转刚度、疲劳寿命测试;
- 运行状态监测:温升、噪声、润滑状态及异常振动信号。
检测方法
1. 外观与尺寸检测
采用目视检查结合三维光学扫描仪,识别裂纹、磨损等表面缺陷;使用高精度三坐标测量仪(CMM)对轴孔直径、键槽对称度等参数进行数字化比对。
2. 动平衡测试
通过动平衡机模拟联轴器实际转速,利用激光传感器采集转子不平衡量数据,并通过去重或配重法实现平衡校正,确保残余不平衡量低于ISO 1940标准要求。
3. 材料性能分析
- 硬度测试:采用洛氏硬度计(HRC)或维氏硬度计(HV)进行多点测量;
- 成分分析:使用直读光谱仪(OES)检测合金元素含量;
- 金相检验:通过金相显微镜观察材料微观组织,评估热处理工艺效果。
4. 动态特性评估
在专用扭矩试验台上模拟实际负载,记录扭矩-转角曲线,计算扭转刚度;通过高频疲劳试验机进行循环加载,评估联轴器在交变载荷下的寿命衰减规律。
5. 运行状态监测
安装振动加速度传感器与红外热像仪,实时采集运行中的振动频谱和温度分布数据,结合AI算法实现早期故障预警。
检测仪器
- 三坐标测量仪(CMM):分辨率达0.1μm,用于高精度尺寸检测;
- 激光动平衡机:最高转速20,000rpm,不平衡量检测精度±0.1g·mm/kg;
- 高频疲劳试验机:载荷范围±50kN,频率可达200Hz;
- 振动分析系统:包含16通道数据采集模块,支持阶次分析与共振频率识别;
- 直读光谱仪:可检测C、Si、Mn等18种元素,分析时间≤20秒。
检测流程优化建议
针对不同工况联轴器,推荐采用分级检测策略:
- 常规巡检:每月进行外观检查与振动监测;
- 中期维护:每12个月开展动平衡校验与材料硬度抽检;
- 大修期检测:每3-5年实施解体检测,包括金相分析和疲劳寿命评估。
结论
联轴器的系统性检测是确保传动系统可靠运行的核心环节。通过建立多维度的检测体系(覆盖几何参数、材料性能与动态特性),结合智能传感器与大数据分析技术,可显著提升故障预警能力。建议企业根据设备关键性等级制定差异化检测周期,同时推动检测数据与设备健康管理系统的深度融合,实现从被动维修向预测性维护的转型升级。
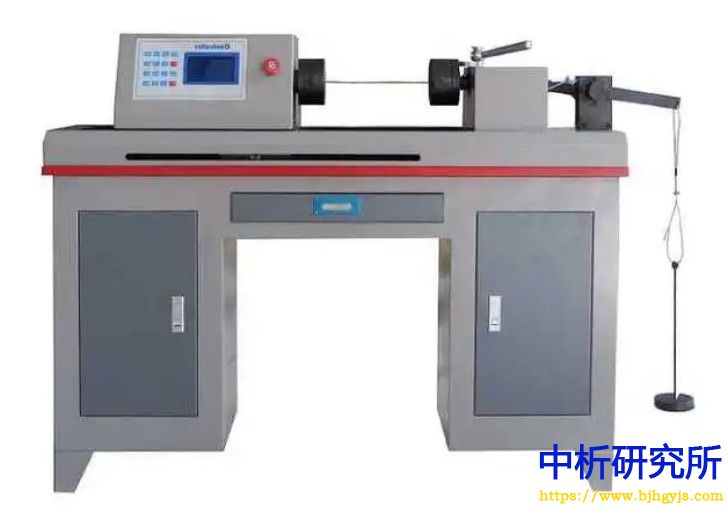
了解中析
实验室仪器
合作客户
